Undergraduate BEng Manufacturing
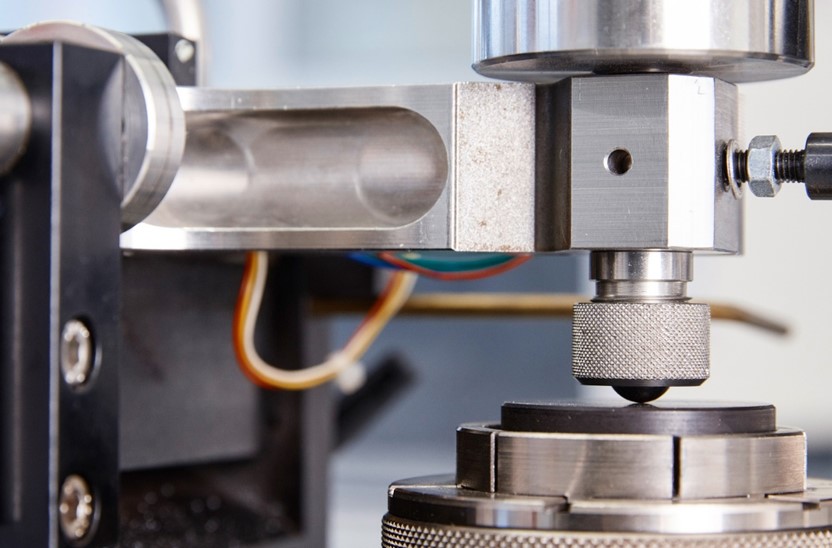
Engineering Tribology
This course provides fundamental understanding for tribological aspects of machine components and mechanical parts including friction, lubrication and wear. Students are exposed to the various tribological behaviour of metallic and non-metallic materials with an aim to apply the knowledge in monitoring and controlling the friction and wear behaviour in practical situations.
Upon completing this course, students should be able to
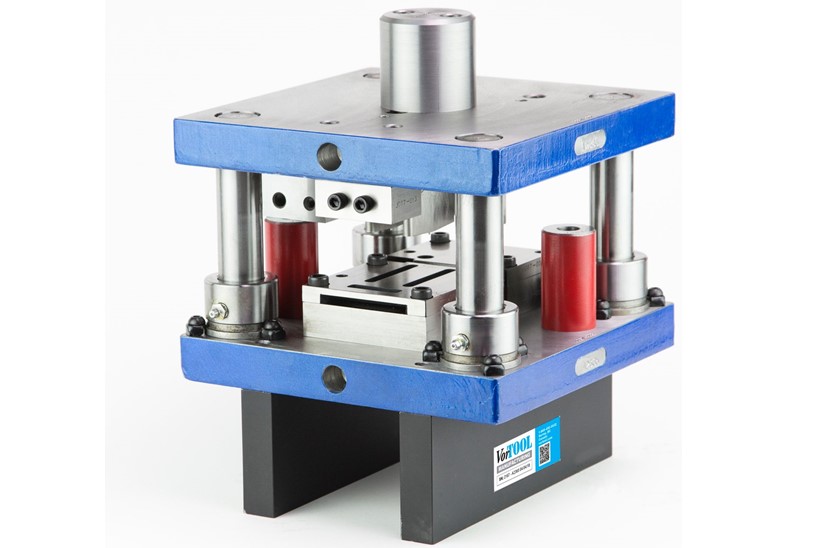
Production Tooling
Types of tooling, tool materials, tool geometry, economics and selection of tooling, single-point tools for turning, hole making, shaping and slotting, classification, selection, design and manufacture of multi-point cutting tools: drills, taps dies, milling cutters, gear cutters, broaches and grinding wheels, principles of jig and fixture design, design and manufacture of tools and dies for sheet metal, plastic moulding, forging and other special applications.
Objectives
Undertake study on the manufacturing aspects of single and multiple point cutting tools.
Provide knowledge on different tool material and tool geometry.
Provide understanding of the locating principle and geometrical aspects of various production tools.
Explain the construction and working principle of jigs, fixtures and dies.
Develop aptitude of designing cutting tools, jigs and fixtures and dies for metal cutting, metal forming and plastic molding operations.
Upon completing this course, students should be able to
Select appropriate tool materials for machining different work materials.
Use proper single point cutting tools for turning, thread cutting, boring, shaping, planning, etc.
Design various tools for thread cutting, gear cutting, hole making and producing flat surfaces.
Select and design different types of jigs for machining parts of different configurations.
Analyze the economic viability of using jigs and fixtures.
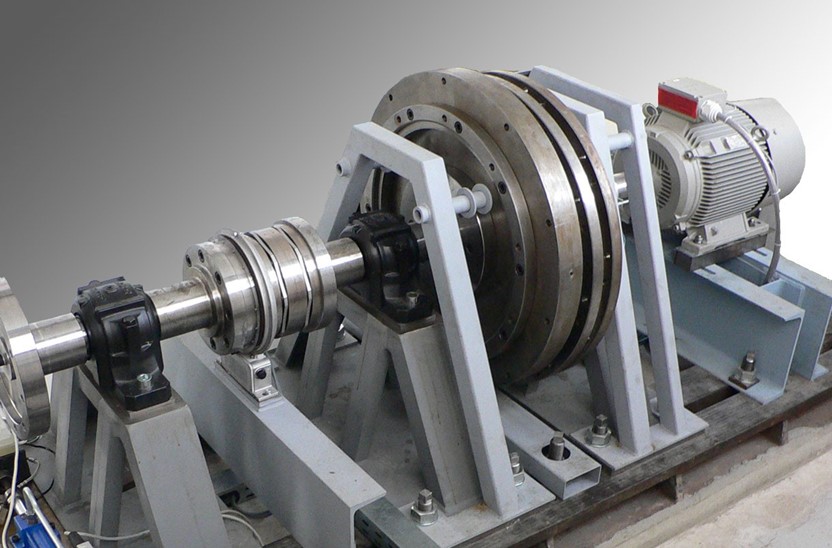
Design of Machine Components
Introduction to stress, strain and strength, Poisson’s ratio, modulus of elasticity, analyses of normal stress, direct shear stress, torsional shear stress and flexural stress, combined stresses, deflection of beams, failure prediction for cyclic and impact loading, design of shafts and associated parts, column, threaded fasteners, springs, selection of rolling bearings, design of belts, chains, wire ropes, gears, brakes and clutches.
Objectives
Introduce students to the concepts of stress and strength.
Introduce students to standard specifications in the design process.
Familiarize students to the effects of forces and torques on elastic bodies.
Expose students to the fundamental theories of machine design.
Introduce students to the design of commonly used machine components for manufacturing.
Upon completing this course, students should be able to
Identify different components of machines and their loads.
Calculate stresses on machine components under static and dynamic loads.
Design machine components on the basis of strength of material and deflection limitations.
Apply standard specifications in the design process.
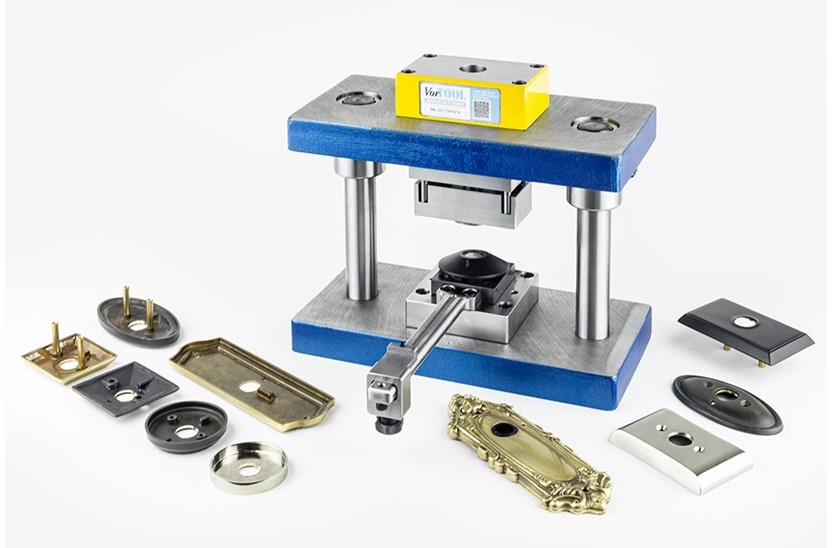
Metal Forming
This course provide the student with fundamental understanding on the theories and numerical methods for analysing complex bulk and sheet metal forming processes. Students are exposed to basic and advanced forming technologies, determining stress conditions of the material deformation during as well as after processing, determining favourable forming process with the right parameters and tool materials, designing metal forming tools, and virtual metal forming processes.
Objectives
Demonstrate basic and advanced technologies of bulk and sheet metal forming processes.
Determine stress conditions of the material deformation during as well as after processing.
Determine favourable metal forming processes with the suitable parameters and tool materials.
Design metal forming tools.
Upon completing this course, students should be able to
Explain basic and advanced technologies of bulk and sheet metal forming processes.
Analyze stress conditions of the material deformation during as well as after processing.
Suggest suitable metal forming processes with the recommended parameters and tool materials.
Synthesis and design tooling for investigated metal forming.
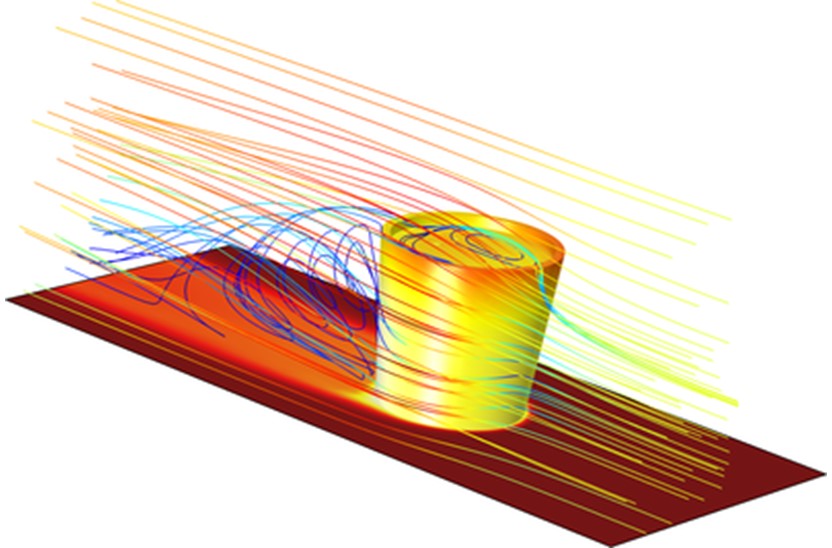
Thermofluids
The course provides fundamental engineering principles of fluid mechanic, thermodynamic, heat transfer, and also applications of thermofluids in Manufacturing Engineering. In Fluid Mechanics attention will be given to the fundamental principles of fluid mechanics and definition, fluid statics, fluid dynamics, and flow over bodies. In Thermodynamics focus is on the fundamental principles of thermodynamics and definition, the Zeroth law, the first law and the 2nd law. In Heat Transfer, different modes through conduction, convection and radiation to be covered.
Postgraduate MSc Manufacturing
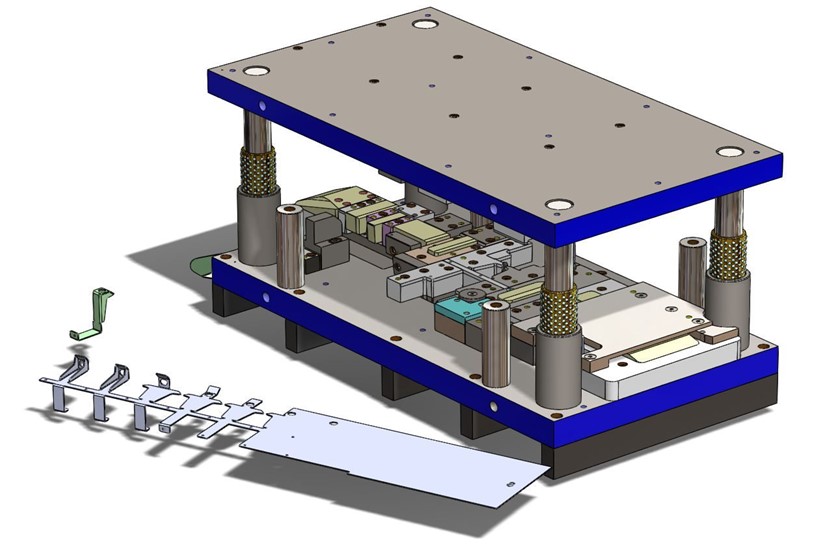
Bulk Deformation and Net Shape Manufacturing
Overview of bulk deformation and net shape manufacturing; stress-strain relationship; elasticity and plasticity; casting; forging, rolling; drawing; deep drawing; sheet metal forming; shearing, bending, spinning; extrusion; injection molding; blow molding; thermoforming; compression molding; hot embossing.
Objectives
Introduce the concept of stress and strain involved in various deformation processes.
Discuss the role of theory of elasticity and plasticity in deformation process.
Deliberate various fundamental principles of material working, and complex forming applications in industry.
Provide the students strong back ground on various net shapes and near net shape manufacturing processes.
Upon completing this course, students should be able to
Explain and apply the relationship between stress and strain in materials deformation.
Simulate for the estimation of optimum parameters in forming and net shape manufacturing.
Relate the strength and properties of materials undergone through various deformation processes.
Design and fabricate products using forming and net shape manufacturing process.