Metal forming involves shaping of metals. By taking advantage of the plasticity of certain metals, the forming process makes it possible to move a metal solid from its current shape into the desired form. Further, it accomplishes this without melting, thereby avoiding any potential difficulties in the handling of molten metal or in the integrity of molded products.
Metal forming is used to create all manner of products, including tubes, pipes, metal sheets, fasteners, wire and much more. Many of the metal objects we encounter in everyday life, from thumbtacks to file drawers, were likely produced by one or more metal forming operations.
Metal forming operations can be categorized as hot, cold or warm working processes. The temperatures involved in these processes are not static, but vary from metal to metal; in some cases, room temperature may mean hot-working conditions. Hot-working involves deforming a metal under conditions above its recrystallization temperature, usually at temperatures higher than 60% of its melting point (Kelvin). For most metals, cold working is typically performed at room temperature or slightly higher temperatures; as long as the temperature of the operation is below the metals recrystallization temperature, it qualifies as cold working. Warm working is performed at intermediate temperatures between those of recrystallization and cold-working.
Hot-working processes include rolling, forging and extrusion. Rolling is also performed as a cold working process, and involves sending metal stock through a set of rollers. The rollers deform the original stock and output it in the preset shape. Sheets, strips, rails and other similar shapes can be produced by rolling. Forging uses presses, hammers and other compressing devices to shape metal stock, and can also be performed cold. Parts made by the cold forging process are often referred to as cold-headed parts. Extrusion is a process whereby stock is forced through a die and emerges as a tube with a nearly identical cross-section.
In addition to forging and cold rolling metal, cold working processes include shearing, drawing and bending. Bending involves the reshaping of metal around a linear axis, while shearing is a chip-free cutting process. Blanking and piercing are both forms of shearing that consist of cutting shapes out of the metal workpiece. Drawing resembles extrusion, except that the workpiece is pulled, not pushed through the dieit is also performed as a hot working process.
Source: Thomas Industry Update.
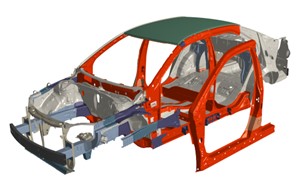
Cold Stamping
In cold stamping, sheet metals are shaped into the desired form using intense pressure. Because pressure is the only method used for forming the new shape, rather than heat, you usually need thicker pieces of metal so that you have to apply more pressure to the sheets.
Cold stamping is faster than hot stamping. In addition, if you need to reform your part or perform processes like draws or flanging, you must use cold stamping. In addition, you have the flexibility to cold stamp parts out of a variety of metals, whereas with hot stamping you only have the option of boron steel.
In cold stamping, you may get springback, resulting in warping of your part. This doesn’t happen with hot stamping because of its high tensile strength and stress-resistance. You also do not get the same ability to manufacture lightweight, complex parts easily as you do with hot stamping.
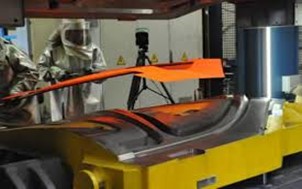
Hot Stamping
In hot metal stamping, the steel blanks are heated until they can be deformed. They are then formed into the proper shape using special dies and are rapidly cooled so that they lock into the desired shape.
Hot stamping allows you to press complex parts with great strength, so you can create a form in a single lightweight piece, rather than having to weld together thicker, heavier parts. This ability to create lightweight parts make hot stamping great for something like manufacturing car frames.
Hot stamp parts also have high tensile strength, which can be a valuable asset.
Hot stamping tends to be a more expensive process than cold stamping. In addition, once a part is formed through hot stamping, it cannot be reformed. You also cannot use hot stamping on all metals. In fact, you must use boron steel for hot stamping, which contributes to its higher cost.
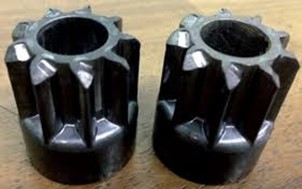
Cold Forging
The cold forging manufacturing process is performed at room temperature. The workpiece is squeezed between two dies until it has assumed their shape. To deliver a finished, ready to fit component, the technique includes rolling, drawing, pressing, spinning, extruding and heading.
Manufacturers may prefer cold over hot forging process; since cold forged parts require very little or no finishing work, which saves cost. The second significant advantage is the material savings achieved through precision shapes. The economic advantages combined with high production rates and long die life are more than enough to convince many manufacturers that cold forging is the best option for them.
Depending on the manufacturer’s requirements, some of the cold forging characteristics may turn out disadvantages; e.g. only simple shapes in high volumes can be shaped. Therefore, if the customer is searching for a specific customized component, cold forging won’t be the best alternative. A second more significant disadvantage is that cold forged metals are less ductile, which makes them inappropriate for certain configurations. Also, because of the grain structure that gives the material its strength, residual stress may occur.
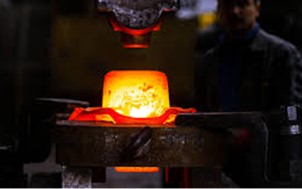
Hot Forging
The hot forging manufacturing process is performed at extreme high temperature (up to 1150 °C for steel, 360 to 520 °C for al-alloys, 700 to 800 °C for cu-alloys). This temperature is necessary in order to avoid strain hardening of the metal during deformation.
Hot forged components possess increased ductility which makes them desirable for many configurations. Also, as a technique hot forging is more flexible than cold forging, since customized parts can be manufactured. The excellent surface quality allows a wide range of finishing work as polishing, coating or painting, tailored to customers’ specific needs.
Less precise dimensional tolerance is a possible disadvantage of hot forged components compared to the cold forged ones. The cooling process should be also performed under special conditions; otherwise there is a risk of warping. Also, the grain structure of forged metals may vary and there is always a possibility of reactions between the atmosphere and the workpiece.